Jak wygląda produkcja płyt chodnikowych
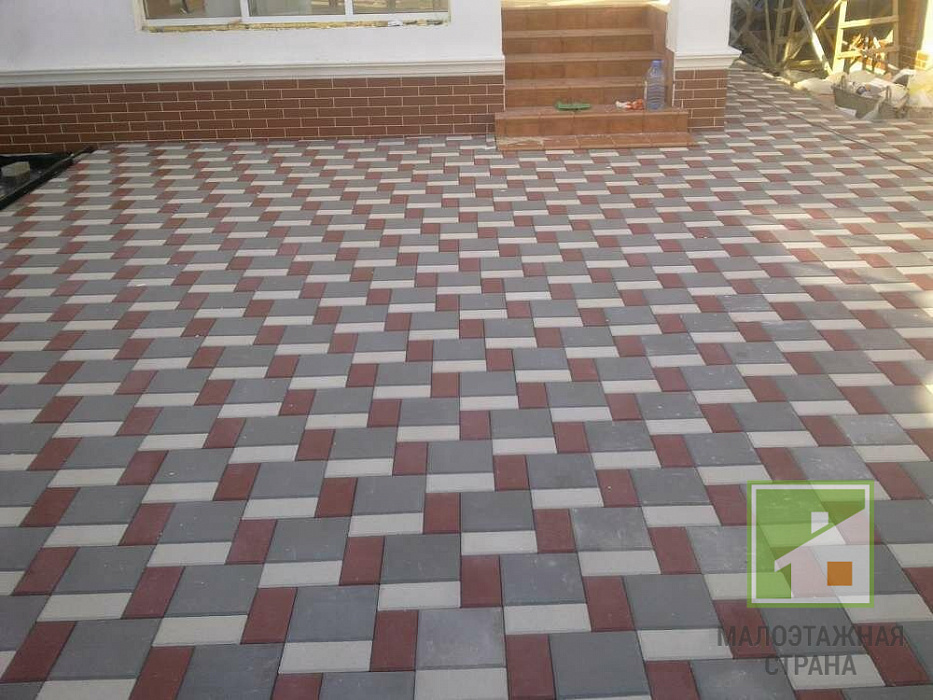
Aby ozdobić witrynę, produkcja płyt chodnikowych odbywa się z dodatkiem barwników lub pokryta wzorem. Istnieje kilka metod jego produkcji, które różnią się kosztem i jakością oryginalnego produktu. Powinieneś także wiedzieć, jakie narzędzia są potrzebne do wykonania płytek i skład zaprawy, która będzie używana w tym procesie. Technologia tworzenia gotowego produktu jest ważną częścią procesu produkcyjnego MES. Od tego zależy wytrzymałość gotowego produktu.
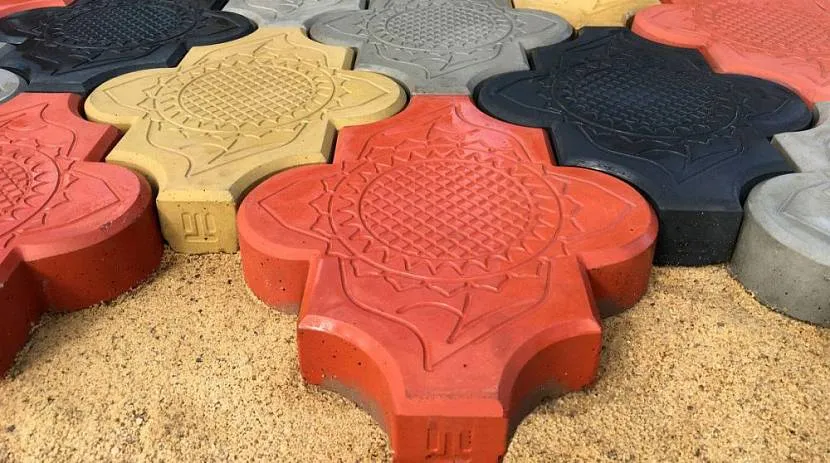
Metody produkcji
Istnieją 2 technologie produkcji płyt chodnikowych:
- Wibroprasowanie to metoda wytwarzania, w której zagęszczanie materiału następuje pod wpływem wibracji i ciśnienia. Ta opcja wymaga komory grzewczej i prasy wibracyjnej. Z ich pomocą płytka jest zagęszczana, a także suszona w wysokiej temperaturze i wilgotności, co zwiększa wytrzymałość materiału. Produkty te służą do układania w miejscach o dużym natężeniu ruchu. Najczęściej ta metoda jest stosowana do dużej produkcji komercyjnej ze względu na wysoki koszt sprzętu.
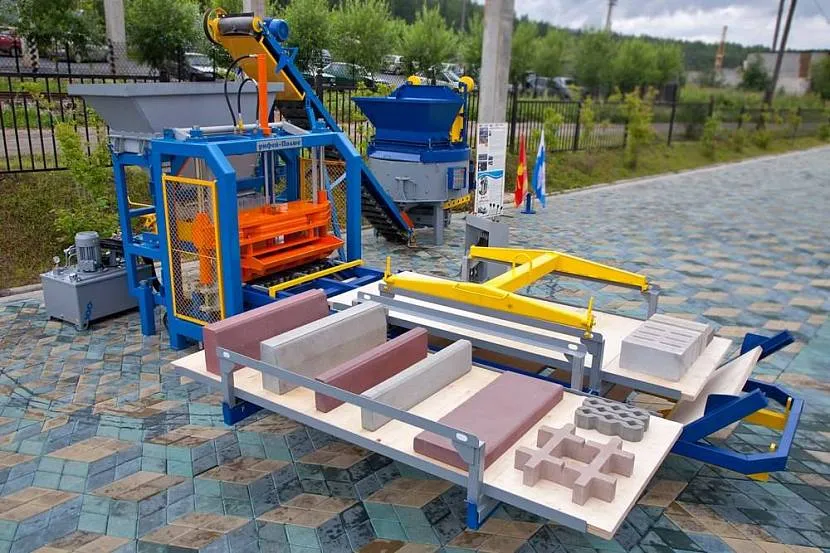
- Odlewanie wibracyjne to metoda produkcyjna potrzebna do produkcji niewielkich ilości płytek. Ta metoda wymaga betoniarki (można ją zastąpić wiertarką z dyszą mieszającą i dowolnym pojemnikiem), form i stołu wibracyjnego. Produkty wykonane w ten sposób nie są przystosowane do dużych obciążeń i najczęściej wykorzystywane są do ścieżek ogrodowych.
Płytka wykonana za pomocą wibroprasy ma chropowatą powierzchnię, a wylana jest gładsza. Różnią się również jasnością i nasyceniem kolorów. W prasowanym produkcie, ze względu na niewielką ilość wody w składzie, barwnik jest słabo rozpuszczalny. Dlatego do dekoracji bardziej nadaje się produkt odlewany.
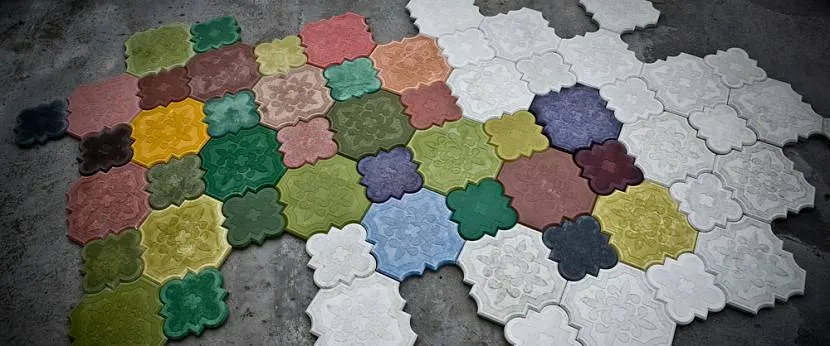
Zaprawa do płytek
Skład zaprawy do płyt chodnikowych, który stosuje się na 1 m2. m produkt o grubości 4-6 cm jest wymagany:
- 20 kg cementu marki M500;
- 30 kg przesianego drobnego piasku (do 2 mm). Zaleca się stosowanie analogu rzecznego ze względu na zawartość wtrąceń wapnia;
- 30 kg drobnoziarnistych skratek granitowych lub tłucznia kamiennego (wielkość od 3 do 8 mm);
- 50 g plastyfikatora C-3 (można zastąpić wapnem gaszonym), co zwiększa mrozoodporność, a także ułatwia proces mieszania i suszenia mieszanki;
- 300-500 g włókna wzmacniającego, które zwiększy wytrzymałość;
- 700 g barwnika w proszku, w zależności od pożądanego nasycenia koloru;
- 14-16 litrów wody, w której należy wcześniej rozpuścić plastyfikator.
Istnieją proporcje zaprawy do płyt chodnikowych, które pomagają wytworzyć niewielką ilość mieszanki:
składniki | Proporcje w % |
Cement | 21 |
Skratki (tłuczeń kamienny) | 23 |
Piasek | 56 |
Pozostałe części są traktowane jako procent całkowitej masy betonu | |
plastyfikator | 0,7 |
Barwnik | 7 |
Włókno wzmacniające | od 0,05 |
Woda | 5,5 |
Przydatne wideo
Przed przygotowaniem roztworu betoniarkę lub inny pojemnik należy umyć wodą w celu zwilżenia ścian. Pomaga to poprawić mieszanie kompozycji, a także ogranicza powstawanie płytki nazębnej. Aby przygotować miksturę, musisz postępować zgodnie z określoną sekwencją:
- Piasek należy dokładnie przesiać z gruzu i korzeni.
- Wymieszaj z cementem.
- Dodaj drobnoziarniste skratki lub żwir, a także włókno wzmacniające.
- Dodaj wodę w częściach, ciągle mieszając całą mieszankę.
Roztwór powinien być gęsty, ale jednocześnie rozprowadzany, wtedy jest gotowy do użycia. Dodatek barwnika następuje na etapie mieszania suchego betonu, ale można zmienić kolor gotowego produktu za pomocą pistoletu natryskowego. Plastyfikator należy wymieszać w gorącej wodzie, aby lepiej się rozpuścił i nie tworzył osadu.
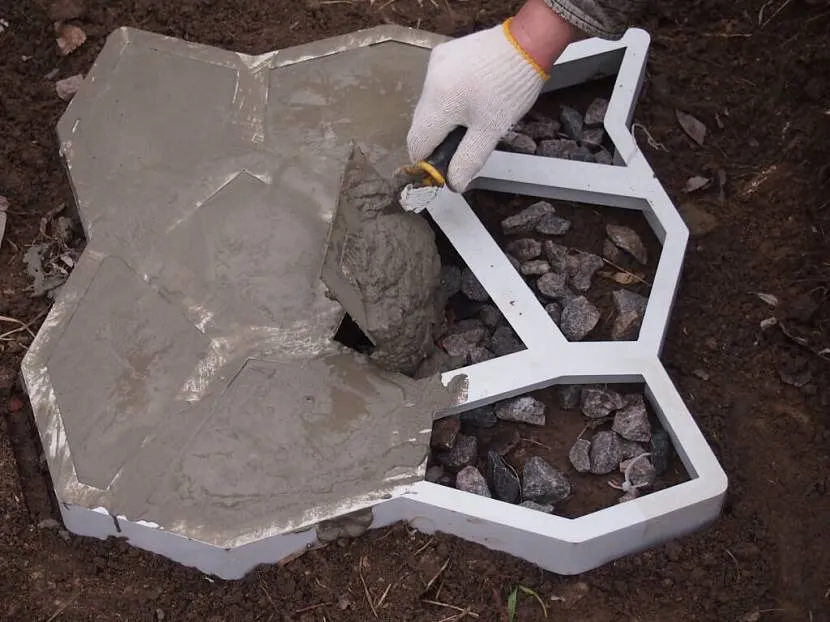
Stół wibracyjny do płytek
W celu usunięcia powietrza i nadmiaru wilgoci z mieszanki betonowej stosuje się stół wibracyjny do płyt chodnikowych. Wykonany jest z wytrzymałej stali. Do łączenia poszczególnych części używane są nity i zgrzewarka.
Platforma wibracyjna jest zamontowana na ramie za pomocą sprężyn tłumiących. Najczęściej wykonany jest z blachy stalowej o grubości 2,5-3 mm. Taka powłoka ma wysoki zasób użytkowania i cenę.
Jeśli stół jest rzadko używany, platforma wykonana jest z płyty wiórowej, płyty OSB lub sklejki. Rama jest zbudowana z rury profilowej lub metalowego narożnika.
Do mocowania silnika stosuje się przyspawane w środku stołu płyty, które wzmacniają konstrukcję. Do platformy wibracyjnej przymocowany jest wał z mimośrodem, który jest osadzony w łożyskach przykręconych do platformy. Jest połączony z silnikiem za pomocą paska, który przekazuje obroty.
Aby wiedzieć, jak zrobić stół wibracyjny i co jest do tego potrzebne, powinieneś przestudiować gotowe opcje i jasno zrozumieć ilość pracy, aby z niego skorzystać.
Przydatne wideo
Główną częścią całej konstrukcji jest silnik. Dostępne są opcje fabryczne, na przykład „platforma wibratora EV-98E” ze zmianą amplitudy oscylacji. Można go zastąpić starym silnikiem z pralki lub szlifierki.
Istnieje również opcja dla małych nakładów pracy, która jest wykonana z opon samochodowych. Są one połączone ze sobą za pomocą wkrętów samogwintujących na wskroś, a wibrator jest zainstalowany w dolnej części zdejmowanej platformy. Aby uniknąć upadku powierzchni roboczej, silnik umieszcza się wewnątrz opon.
Stół wibracyjny można wyposażyć w specjalne sito do przesiewania piasku, co pomoże przyspieszyć pracę.
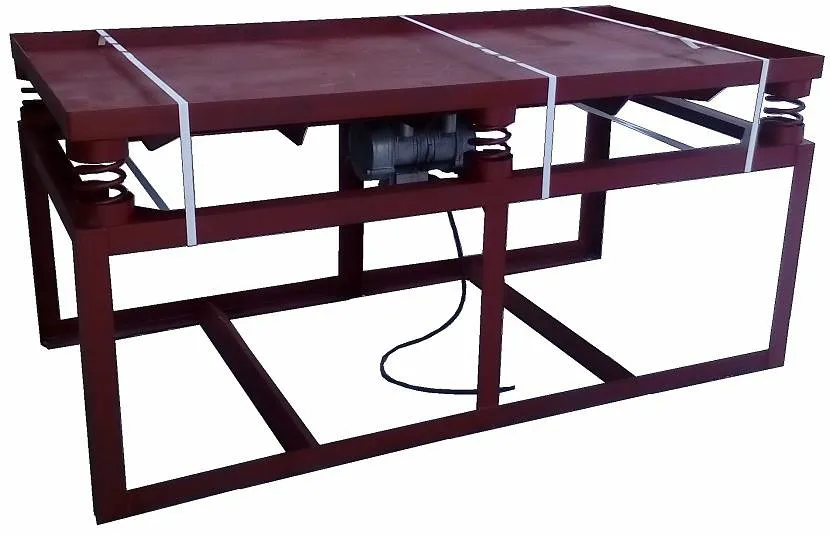
Technologia wytwarzania metodą wibrocastingu
Do produkcji gotowego produktu wymagane jest przygotowanie wszystkich narzędzi i mieszanek. Przed wlaniem betonu do form smaruje się je roztworem usprawniającym rozszalowywanie (usunięcie płytki z formy). Stosuje się gotowe preparaty lub analog 50 gramów oleju silnikowego i 1500 gramów wody.
Zamiennik należy długo i dokładnie mieszać, ponieważ oba płyny mają różną gęstość. Jeśli roztwór jest zbyt tłusty, na płytce pojawią się duże pory, które wyglądają jak muszla. Kompozycja z niewielką ilością oleju nie pozwoli na normalne zdzieranie. Same formularze są używane na kilka sposobów:
- Plastikowy. Pojemnik o dowolnym kształcie, który można kupić w sklepie lub zastąpić podobnym pojemnikiem.
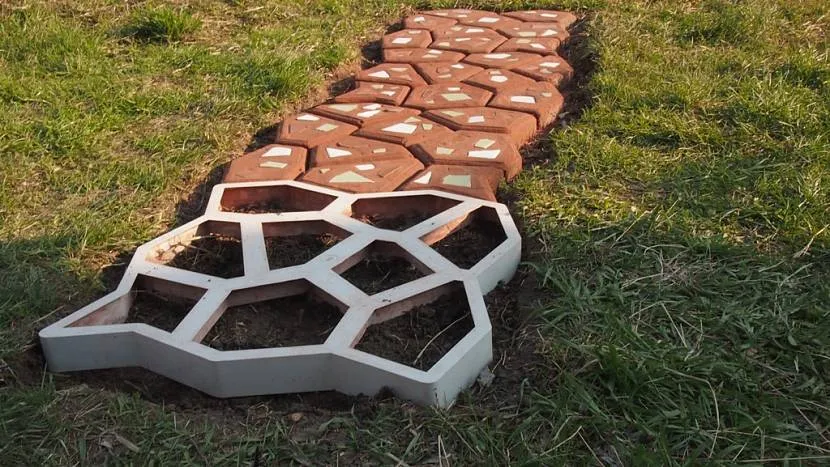
- Silikonowa guma). Plastikowy i elastyczny odpowiednik formy do tworzenia płytek. Za ich pomocą możesz skopiować wzór gotowej powłoki. W tym celu dostępny jest wybór gotowych mieszanek silikonowych.
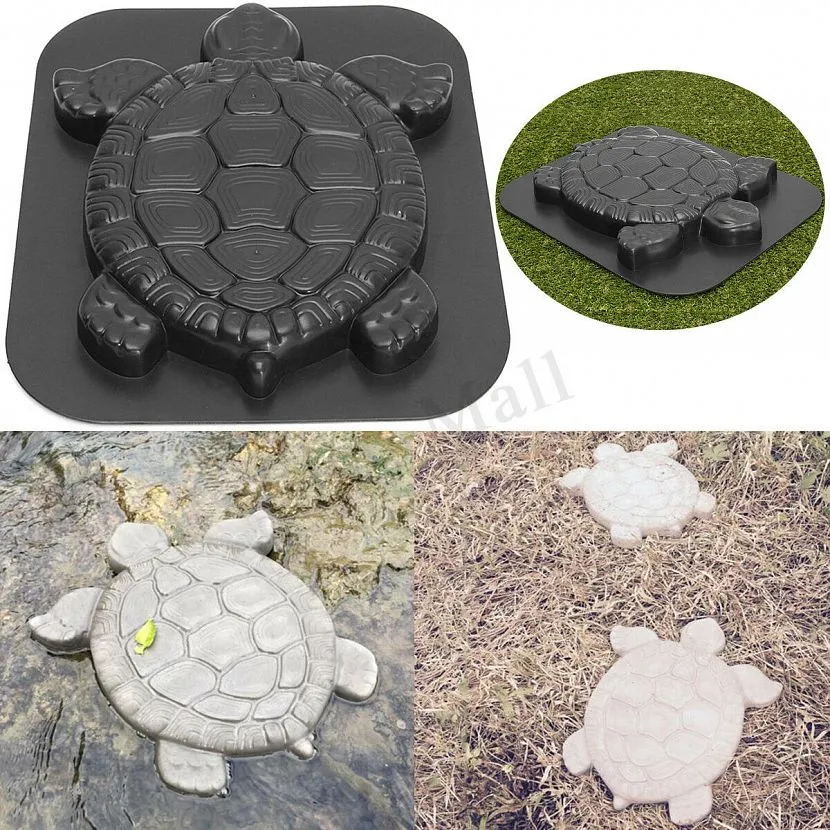
- Z drewna. Wykonane są ze sklejki odpornej na wilgoć. Układa się go na dnie, a szalunek wykonany jest z prętów, które są połączone wkrętami samogwintującymi lub metalowymi narożnikami za pomocą śrub. Takie formularze są przeznaczone tylko dla prostych figur.
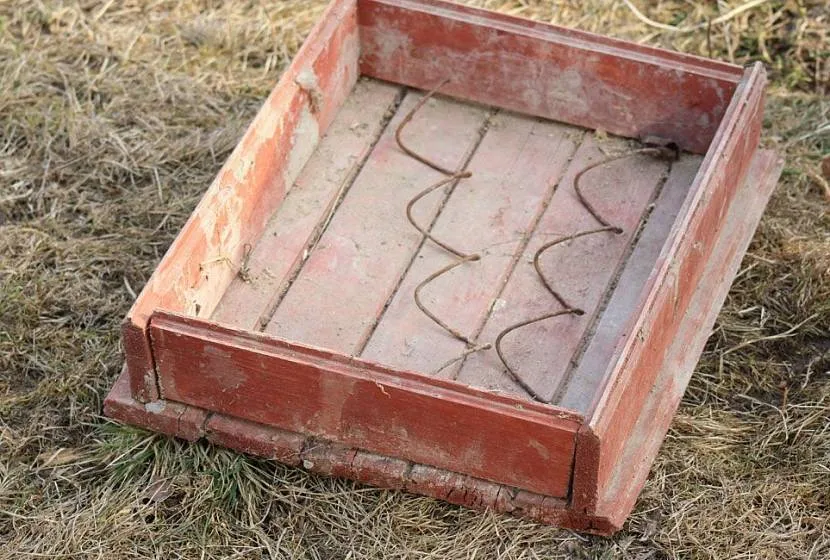
- Metal. Aby je stworzyć, potrzebujesz spawarki. Takie formy są najmocniejsze i najtrwalsze, ale są ciężkie, a ich złożenie wymaga dużo czasu i środków.
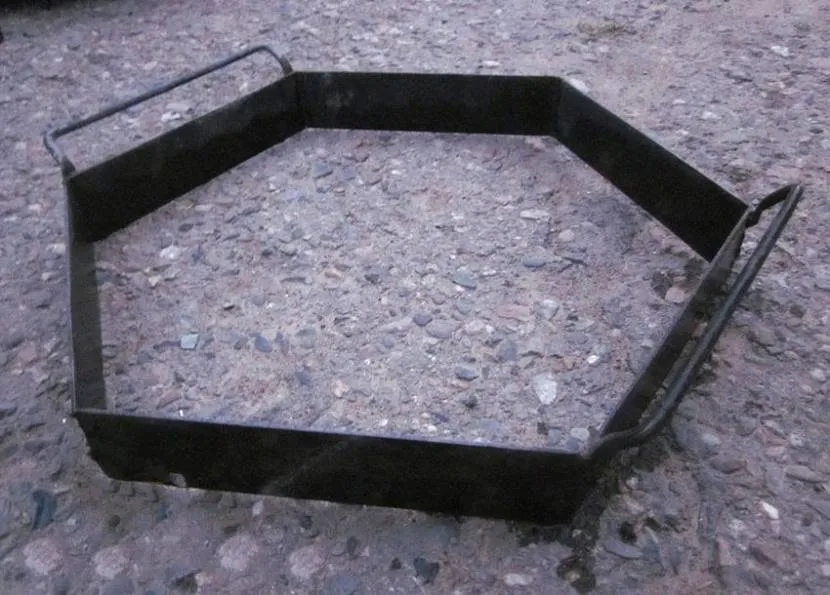
Do przygotowanych form wlewa się roztwór do płyt chodnikowych, który należy wygładzić szpachelką lub kielnią. Następnie pojemniki umieszczane są na stole wibracyjnym. Ważne jest, aby nie przeciążać urządzenia, ponieważ wtedy nie będzie ono wibrować z żądaną częstotliwością.
Po włączeniu silnika wilgoć zaczyna rosnąć, a sama mieszanka płyty chodnikowej zaczyna się zagęszczać. Z tego powodu w formularzach jego ilość wizualnie się zmniejszy i powstanie dodatkowa przestrzeń, którą należy wypełnić roztworem.
Wymagane jest trzymanie pojemników na stole przez 4-5 minut, aż pojawi się biaława piana. Oznacza to, że całe powietrze jest poza mieszanką. Następnie należy go przenieść w suche miejsce, w którym nie ma światła słonecznego. Ze względu na plastyfikator i niską zawartość wody płytka schnie w ciągu 24 godzin.
Wysuszony produkt należy wyciągnąć z foremek i pozostawić na 4-5 dni, aby zwiększyć wytrzymałość. Formy po oszalowaniu należy umyć solą fizjologiczną, aby usunąć pozostałą mieszaninę. Pozwala to przedłużyć żywotność pojemników do dalszego użytkowania.
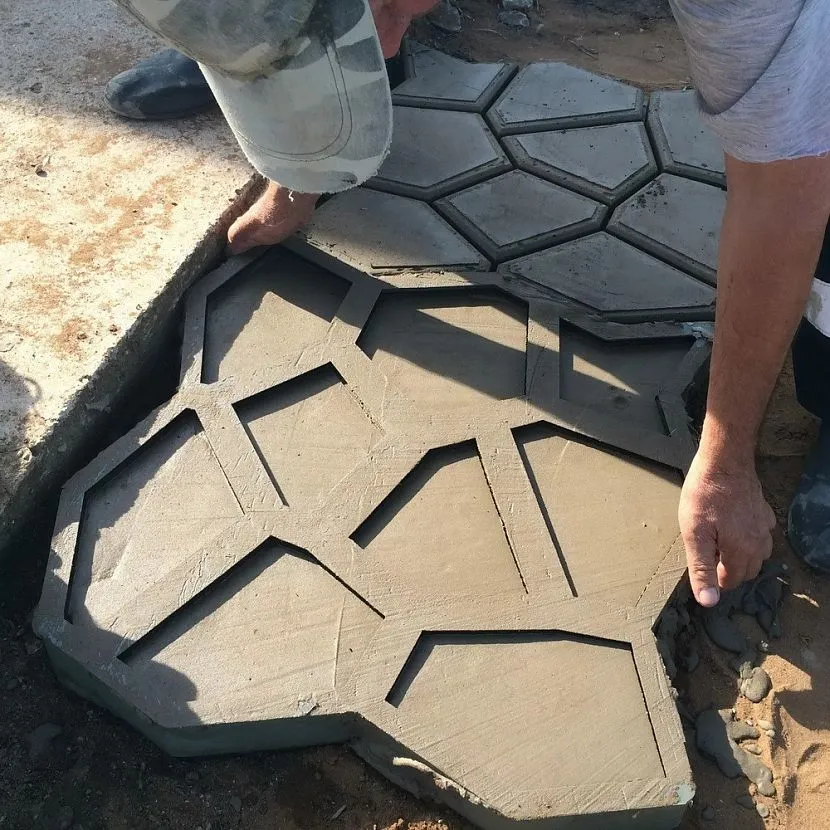
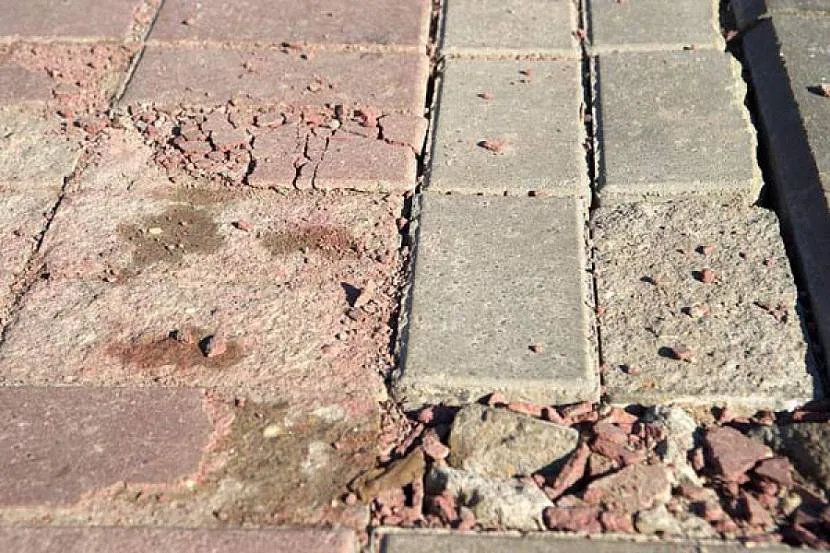
Zalety płyt chodnikowych
Wśród pozytywnych cech płyt chodnikowych wyróżniają się:
- Odporne na wilgoć. Po deszczu cała woda trafia do szwów lub wypływa z powierzchni, co pozwala uniknąć powstawania kałuż, a zimą również lodu.
- Czystość ekologiczna. Podgrzane na słońcu płytki nie wydzielają szkodliwych oparów ani chemikaliów.
- Niezawodność. Prawidłowo wykonany produkt może przetrwać ponad 15 lat i wytrzymać duże obciążenia (do 600 kg na cm2).
- Łatwość naprawy. Każdą sekcję, która uległa awarii, można zastąpić podobnym nowym elementem bez zmiany całej konstrukcji.
- Wygląd zewnętrzny. Dzięki szerokiej gamie kształtów, kolorów i wzorów możesz stworzyć niepowtarzalny styl pokrycia witryny.
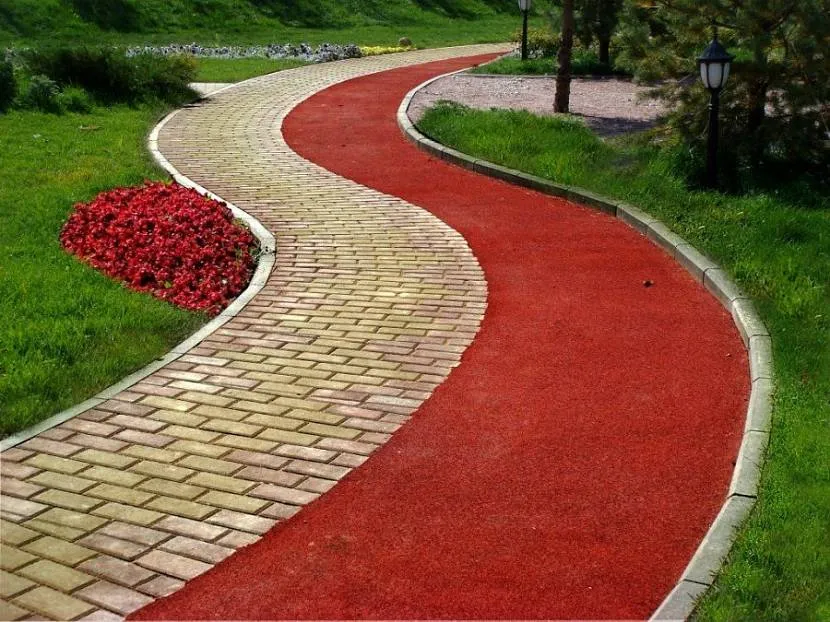
Wymagania dotyczące płyt chodnikowych
Podstawowe wymagania dotyczące płyt chodnikowych:
- Wytrzymałość betonu na ściskanie. Jest oznaczony jako B24, gdzie B to klasa wytrzymałości, a 25 to minimalne obciążenie, jakie konstrukcja może wytrzymać (25 MPa lub 254 kgf / cm2). W przypadku płytek obowiązują klasy od 22,5 do 40.
- Odporność na mróz. Oznaczona jest co najmniej F200, gdzie F to stopień mrozoodporności, a 200 to liczba cykli zamrażania i rozmrażania (od -20 do +20 °C).
- Przetarcie. Pokazuje, jak bardzo zmieni się objętość i waga płytki pod wpływem tarcia. Stosowane jest oznaczenie G1 (nie więcej niż 0,7 g na cm²)
- Grupa operacyjna. Podzielone w zależności od wpływu obciążeń podczas użytkowania: A – chodniki dla pieszych i ulic, B – przystanki komunikacji miejskiej lub ścieżki rowerowe, C – parkingi, stacje benzynowe i drogi o małym natężeniu ruchu, D – terminale kontenerowe lub magazyny.
- Absorpcja wody. Wpływa na żywotność płytki, ponieważ przy wysokim procencie nasiąkliwości może pękać podczas zamrażania i rozmrażania. Wilgotność nie powinna przekraczać 5-6% masy produktu.
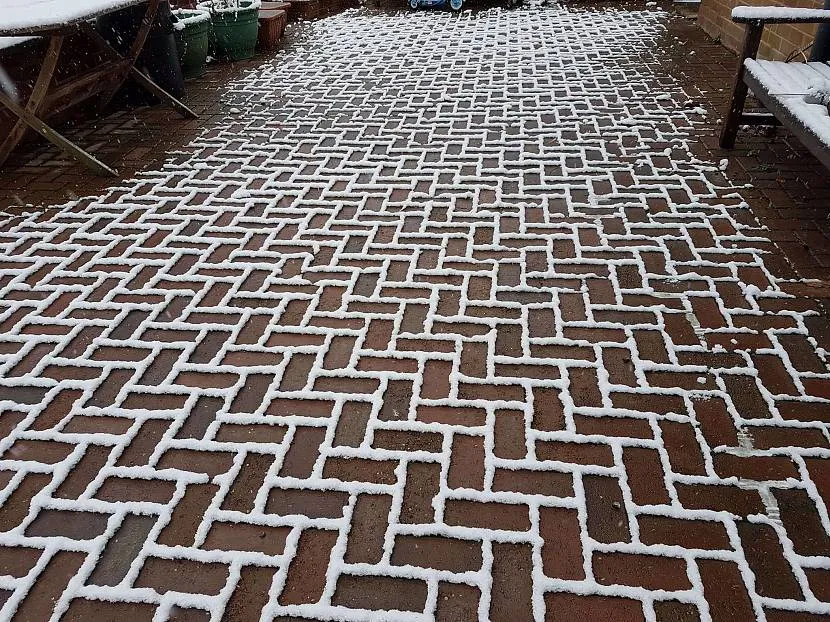
Ponadto w składzie płyt chodnikowych podczas ich produkcji powinna znajdować się minimalna ilość wilgoci, ponieważ ma to bezpośredni wpływ na jej wytrzymałość.
Przydatne wideo
Podsumowanie
Istnieją 2 metody wytwarzania płyt chodnikowych: wibroprasa i wibrocasting.
Przy produkcji betonu należy wziąć pod uwagę proporcje i kolejność mieszania, ponieważ ma to duży wpływ na wynik końcowy.
Zaleca się wykonanie stołu wibracyjnego do płytek z trwałego żelaza, a także użycie silnika fabrycznego. Zwiększy to zasoby pracy i produktywności.
Suchą płytkę, która właśnie została wyjęta z formy, zaleca się stosować dopiero po 4-5 dniach, ponieważ wcześniej będzie mniej wytrzymała.