Spawanie pulsacyjne: technologia, odmiany
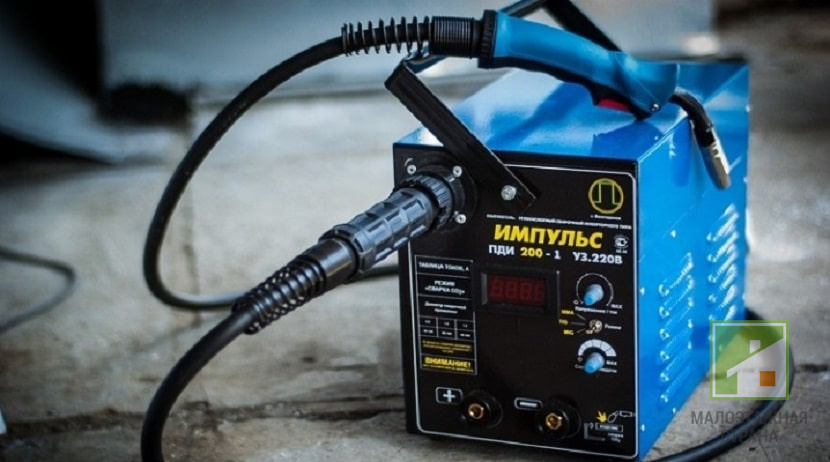
Definicja „spawania łukiem impulsowym” dokładnie oddaje jego zasady funkcjonalne, w których impulsy prądowe (Pulsy prądowe) nakładają się na główny prąd tła (Prąd tła) z określoną częstotliwością, jako dodatek. W technologii produkcji metoda ta jest jednym z rodzajów spawania łukowego (Arc Welding), szeroko stosowanym w przemyśle.
Technologia spawania impulsowego
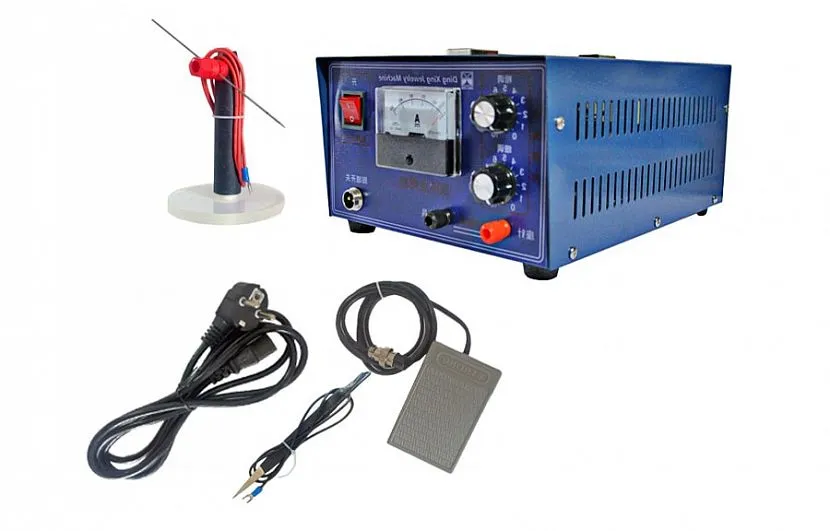
Spawanie pulsacyjne (Pulse Welding), jak wspomniano powyżej, jest łukiem, tylko w tym przypadku łuk jest chroniony osłoną gazową. Przy narzucaniu prądu pulsującego na prąd spawania, ten drugi stanowi tylko 10-15% tego pierwszego. Istnieją również rozwiązania z podwójnym impulsem (Double Impulse), gdzie występuje modulacja impulsowa, pozwalająca na zmianę kształtu, kąta i czoła fali, co powoduje korekty w przenoszeniu małych kropel metalu podczas pracy. Jedną z cech definicji spawania łukiem impulsowym można nazwać oscylacjami przemiennych impulsów o częstotliwości do 250 Hz.
Takie cechy spawania pulsacyjnego umożliwiają zwiększenie obciążenia mocy, co z kolei minimalizuje prawdopodobieństwo niespawanych odcinków szwu, a także prowadzi do oszczędności w materiale wypełniającym. W tym przypadku łuk główny lub podstawowy jest przerywany na czas trwania impulsu, czyli ma ustawiony przez program tryb włącz/wyłącz, który uwzględnia również rodzaj metalu, grubość krawędzi jako wielkość i położenie (pionowe, poziome) jeziorka spawalniczego. Okazuje się, że przedmiot obrabiany jest topiony pod wpływem wysokiej temperatury łuku, a następnie przenoszony do kąpieli z niewielkim lub żadnym rozpryskiem. Pomimo wysokiej wydajności cieplnej, technologie tego typu pozwalają uniknąć przepaleń metalu.
Odmiany spawania pulsacyjnego
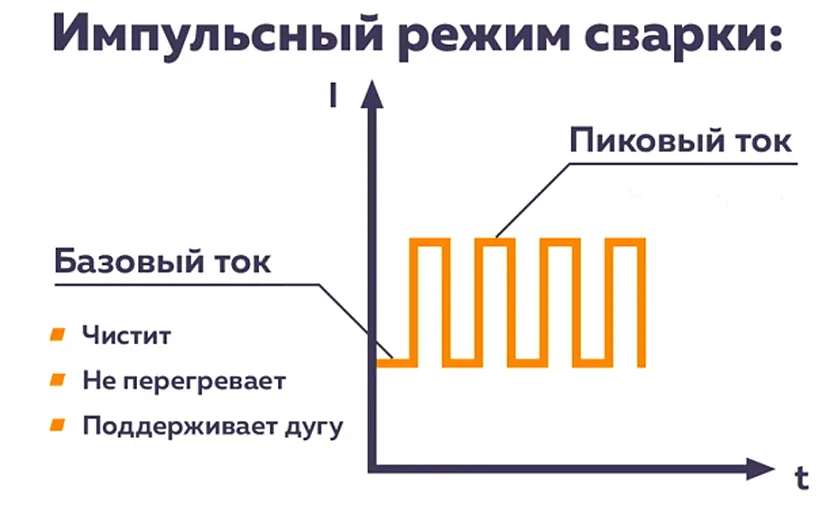
Metale mają różne temperatury topnienia, co wymaga innego podejścia, a dziś istnieją cztery rodzaje spawania pulsacyjnego MIG:
- Spawanie kondensatorem lub kondensatorem impulsowym (CPW). Spawarki tego typu wyróżniają się szeroką gamą wskaźników natężenia i mocy prądu. CPW stosuje się głównie do spawania odłamków aluminiowych.
- Spawanie impulsem magnetycznym lub spawanie impulsem magnetycznym. Takie urządzenia są stosowane w przypadkach, gdy spawanie fragmentów odbywa się pod wysokim ciśnieniem wytwarzanym przez pole magnetyczne, to znaczy, że dokowanie przebiega z jednoczesnymi efektami termicznymi i magnetycznymi. Takie jednostki są używane nie tylko do jednorodnych części, ale także warzone są różne metale.
- Spawanie inercyjne lub spawanie inercyjne działa za pomocą koła zamachowego napędzanego silnikiem elektrycznym. Rezonans bezwładności powstaje w wyniku energii kinetycznej pochodzącej z koła zamachowego.
- Spawanie akumulatorowe lub spawanie bezprzewodowe. Spawanie łukiem impulsowym typu akumulatorowego różni się od pozostałych brakiem poboru mocy podczas pracy urządzenia. W półautomatach awarie, takie jak zwarcie, które występuje, gdy łuk tworzy się między elektrodą lub drutem elektrodowym a szwem, są natychmiast stabilizowane. Urządzenia te zwykle korzystają z baterii alkalicznych.
Spawanie mikroimpulsowe
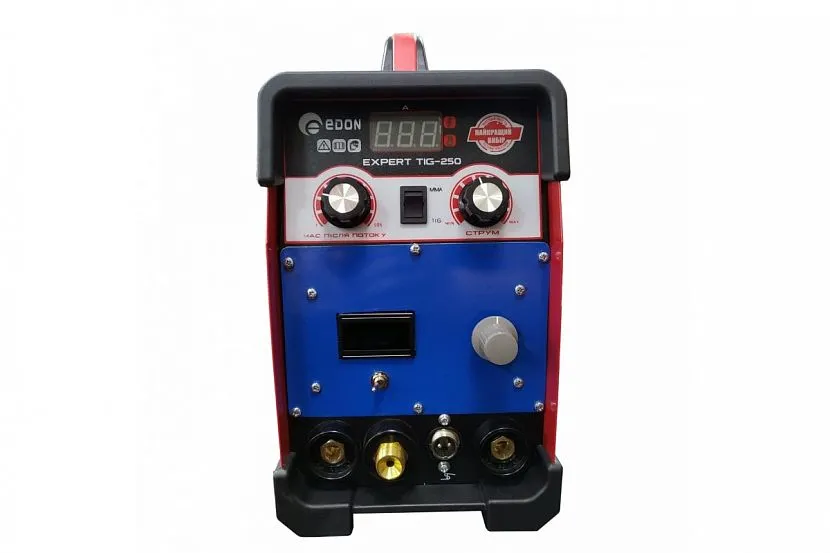
Spawanie łukowe mikroimpulsowe jest stosowane do pracy z dentystycznymi stopami tytanu (Dental Titanium Alloys) w protetyce. Takie rozwiązania, zdaniem dentystów i techników, nie są gorsze od urządzeń laserowych - w obu przypadkach, po zadokowaniu, uzyskuje się połączenie wysokiej jakości, w którym nie jest już potrzebna dodatkowa obróbka powierzchni. Oprócz gabinetów dentystycznych, pulsacyjne zgrzewanie punktowe tego typu znajduje zastosowanie w ortopedii (przeważnie są to duże ośrodki o tym kierunku).
Zalety i wady urządzeń impulsowych
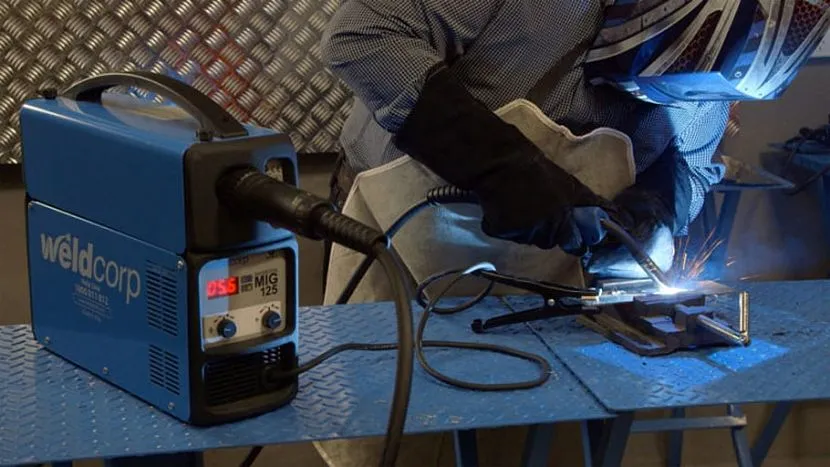
Jak każde inne spawanie pulsacyjne MIG ma swoje pozytywne i negatywne strony, a teraz spójrzmy na pasek z plusami:
- wysoka prędkość szycia;
- możliwe jest łączenie bardzo cienkich części wykonanych z aluminium (grubość 1 mm);
- szew spawalniczy po spawaniu łukiem impulsowym jest wysokiej jakości;
- zawsze można kontrolować zarówno minimalizację, jak i krystalizację metali;
- deformacja szwu jest praktycznie nierealna lub w każdym razie jest zminimalizowana;
- metal nigdy się nie wypala, pomimo wysokich temperatur;
- istnieje możliwość zaoszczędzenia pieniędzy na drucie elektrodowym i gazie, czyli na materiałach eksploatacyjnych;
- pozycje robocze zawsze pozostają stabilne;
- możliwe jest monitorowanie początku topnienia (zakładana jest precyzyjna kontrola);
- podczas rozruchu nie może wystąpić zwarcie;
- stopiony metal nie rozpryskuje się, a dym praktycznie się nie pojawia.
A teraz zwróćmy uwagę na wady spawania impulsowego - należy je koniecznie wziąć pod uwagę przed pracą:
- konwerter impulsów może się przegrzać;
- spawanie impulsowe pozwala na pracę tylko z niewielką powierzchnią łączonych części;
- nie ma specjalnych modyfikacji urządzeń do użytku domowego;
- istnieją pewne trudności w opiece i utrzymaniu;
- dość wysokie ceny za różne modele.
Tak czy inaczej, ale sam widzisz i możesz być przekonany w praktyce, że spawanie pulsacyjne ma więcej pozytywnych aspektów niż negatywnych.
Aplikacje
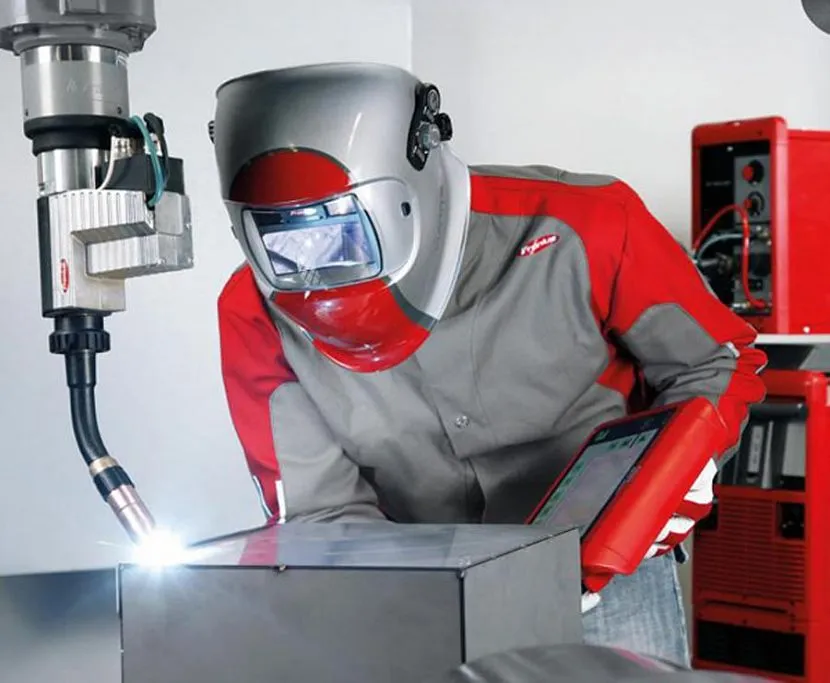
Oczywiście spawanie impulsowe dotyczy przede wszystkim technologii przemysłowych i jest najczęściej stosowane przy układaniu metalowych rurociągów wysokociśnieniowych. W takich projektach maksymalna wytrzymałość złącza jest uważana za niezbędny czynnik, który nie toleruje żadnych zmian ani tolerancji. Obowiązuje tutaj norma międzystanowa GOST 16037-80, która określa wszystkie wymagania dotyczące łączenia i wytrzymałości szwów między rurami stalowymi.
Zakresy zastosowania spawania łukiem impulsowym:
- takie spawanie jest stosowane w inżynierii mechanicznej do karoserii samochodowych;
- jest potrzebny przy montażu różnych dźwigów i sprzętu do robót ziemnych;
- w transporcie kolejowym spawanie pulsacyjne stosuje się do montażu jednostek trakcyjnych (lokomotyw spalinowych, lokomotyw elektrycznych) i wagonów;
- w przemyśle stoczniowym jest potrzebny do poszycia kadłubów dużych i małych transportów;
- stosowany w budowie mostów i różnych nośnych konstrukcji stalowych poddawanych dużym obciążeniom mechanicznym;
- w medycynie - protetyce i ortopedii.
Przydatne wideo
Wniosek
Spawarki MIG występują w różnych typach, co pozwala im pracować z metalami żelaznymi, nierdzewnymi i nieżelaznymi o grubości od 1 do 50 mm, a jednocześnie wykonywać szwy o dowolnej złożoności. Takie technologie są oczywiście przeznaczone dla obiektów przemysłowych i serwisów samochodowych, ale mimo to, pomimo braku specjalnych modyfikacji, niektóre modele znajdują się w małych warsztatach domowych, gdzie są z powodzeniem stosowane.